INTRODUCTION
Commercial isotactic polypropylene (iPP) with at least four basic crystalline modifications, i.e., monoclinic α-crystal, trigonal β-crystal, orthorhombic γ-crystal and smectic mesophase,[1,2] is a classic thermoplastic with tremendous industrial application value due to its excellent comprehensive properties. Among the above crystalline phases, β-crystal shows the excellent toughness and ductility, and thus attracts the most academic interest and industrial applications. Nevertheless, its formation needs certain conditions, including abrupt temperature gradient,[3] elongation or shearing deformation[4-6] and β-nucleating agent (β-NA).[7] Among the above approaches, the introduction of β-NA is regarded as the most efficient and reachable strategy.
During practical polymer processing, there exists elongation/shear flow fields, which profoundly affects orientation, nucleation and consequent crystallization of polymer.[8,9] However, unlike “weak” shear flow field, elongation is much more effective in promoting the formation of oriented structures and thus enhancing tensile strength.[10] Naturally, the combination of β-crystal generated via β-NA and orientation crystallization induced by stretching is supposed to be capable of simultaneously reinforcing and toughening iPP parts. In fact, due to complicated flow field in practical extrusion process, it is not easy to be realized.[11] During practical extrusion process, there is a complicated and inevitable stretching flow field, including shearing in extrusion barrel or die and stretching after leaving the die exit. However, the influence of stretching in extrusion barrel or die on orientation crystallization is not clear. Herein, to tremendously reduce flow field in barrel and die, the speed of screw rotation was slowed down to 0.6 r/min, which is different from that in literature.[11,12] Therefore, stretching after leaving the die exit can be considered as principal factor manipulating orientation crystallization in samples.
The major aim of this study is to investigate the evolution of crystallization behavior and mechanical properties upon various β-NA contents and strong elongation flow field. Furthermore, the relationship between crystallization structure and tensile properties is established. Noting that β-crystal content gradually increases with the augment of β-NA content even though the elongation flow field is relatively strong. Interestingly, the tensile properties of iPP film containing 0.05 wt% β-NA is higher than those of other films, indicating the simultaneously enhanced toughness and tensile strength.
EXPERIMENTAL
Materials
Commercial iPP (T30S) used in this work was purchased from Lanzhou Petroleum Chemical Co., China. Its
Sample Preparation
The iPP pellets and various β-NA contents were blended in a twin screw extruder (SHJ-20B). During blending process, the temperatures were 150, 160, 170, 185, 195 and 190 °C from hopper to die. Subsequently, the pelletized and dried droplets were extruded via a single screw extruder (i.e., Haake Polylab System-Rheomex 252p series) through a slit die (1×50 mm). Moreover, temperature profiles were 165, 180, 195 and 185 °C from hopper to die, respectively. For the sake of minimizing shear stress in die, screw speed of extruder was controlled at 0.6 r/min. Therefore, melt flow rate in die was exceedingly small (ca. 0.9 cm/min) and thus the influence of shear stress can be ignored. During the extrusion process, iPP or β-nucleated iPP melt was stretched under a constant stretching rate of 90 cm/min once it left die exit of extruder. Schematic of films process and a typical photo of them are presented in Figs. S1(a) and S1(b) (in the electronic supplementary information, ESI). All take-up rollers were kept at ca. 25 °C (i.e., room temperature). For simplicity, the obtained films were named as iPP90-y, where y refers to β-NA content. The thickness of melt-stretched films is about 28−30 μm.
Characterizations
Mechanical properties
Mechanical performances of specimens were assessed via a SUNS Universal tensile testing machine. According to ASTM D638-03, the crosshead speed was set at 30 mm/min. During the testing process, the gauge length of samples was 16 mm. All dumbbell-shaped specimens (see Fig. S1c in ESI) were cut in the center of above films using a cutting knife along stretching direction. For every composition, at least five specimens were tested and the experimental results of tensile parameters were evaluated as average of them.
X-ray measurements
Two-dimensional small-angle X-ray scattering (2D-SAXS) and two-dimensional wide-angle X-ray diffraction (2D-WAXD) experiments were conducted in Shanghai Synchrotron Radiation Facility (SSRF). A MAR 165 CCD X-ray detector was used for collection of 2D-SAXS and 2D-WAXD images. The chosen X-ray wavelength and X-ray resolution of this detector were 0.124 nm and 2048 pixel × 2048 pixel, respectively. The distance between this detector and sample for X-ray measurements was 5200 mm and 178 mm for 2D-SAXS and 2D-WAXD, respectively. Moreover, several pieces of iPP or β-nucleated iPP films were accumulated orderly with final thickness of ca. 1 mm so as to get maximum diffraction intensity. All the data were treated with FIT2D software.
Differential scanning calorimeter (DSC)
A DSC (TA-2920) instrument was employed to study the melting and crystallization behaviors of films. The DSC measurements were carried out in nitrogen atmosphere. As illustrated in Fig. S1(b) (in ESI), specimens (ca. 6 mg) were heated at a heating rate of 10 °C/min from 25 °C (i.e., room temperature) to 200 °C. To eliminate the heat history, specimens were kept for 5 min at 200 °C and then cooled at the same cooling rate of 10 °C /min.
Atomic force microscopy (AFM)
An AFM (Bruker, Multimode 8) was employed to observe the topography of films in tapping mode. All experiments were performed in air at about 25 °C (i.e., room temperature). All the data were treated with NanoScope Analysis1.5 software. The crystalline morphologies distinguished from height and amplitude images were collected.
Polarized optical microscopy (POM)
The morphology development of films during non-isothermal crystallization was investigated via a POM (Olympus BX-51). Specimens for POM observation were cut from the center of films. These specimens were placed in the hot stage, and each was heated to certain melting temperature and kept for 5 min at this temperature. Then, the specimens were cooled to 40 °C at a cooling rate of 10 °C/min, and thus during non-isothermal crystallization process, the crystallization morphology was recorded via POM. For comparison, the crystallization morphology development at the same conditions of iPP film prepared at relatively lower stretching rate was observed, and the results are shown in Fig. S6 (in ESI).
RESULTS AND DISCUSSION
Mechanical Properties of Films
Fig. 1 shows the typical stress-strain curves and quantitative estimated mechanical properties (strain energy density at break, Wb; tensile strength, σ; elongation at break, ε) of films. As well known, σ of iPP is about 35 MPa.[12,14,15] Herein, σ for all films is higher than 50 MPa. In addition, compared with iPP90-0, both ε and Wb of β-nucleated films are improved significantly. Unexpectedly, σ, ε and Wb of iPP90-0.05 are 68.5 MPa, 1064% and 524.1 MJ/m3, respectively, which are the maxima. Nevertheless, σ of iPP90-0.2 is higher than that of iPP90-0.1. Since tensile properties of samples are mainly influenced by their microstructure, in the following scenario, systematic characterizations will be conducted to investigate thoroughly the correlation between tensile properties and microstructure.
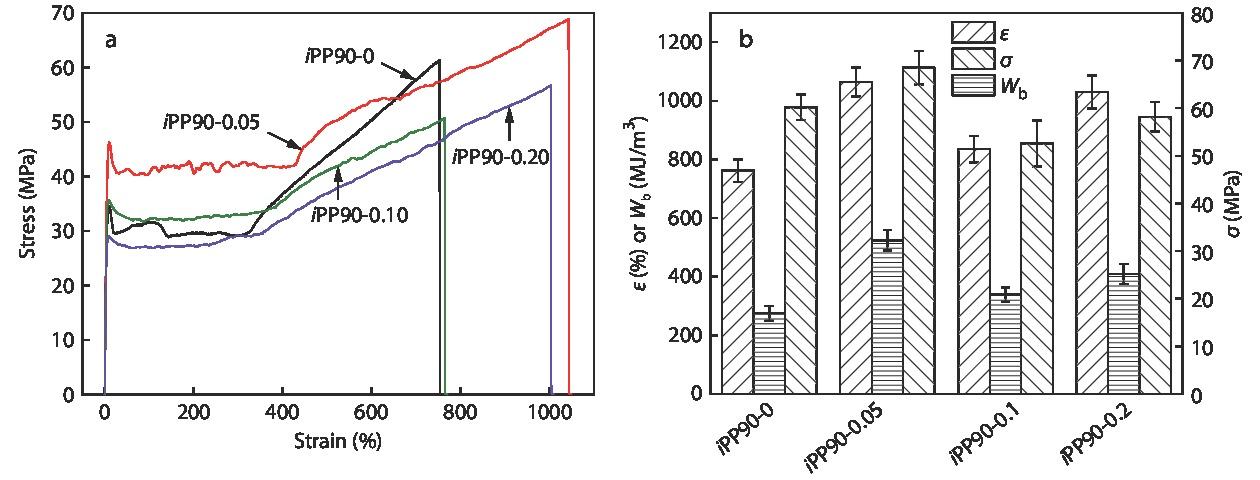
Crystalline Structure
Fig. 2 shows the 3D-WAXD, 3D-SAXS images and their corresponding curves of films. As can be seen, evident arc-like diffractions of lattice plane (Fig. 2a) and an intensive two-spot pattern in meridional direction (Fig. 2b) for all films are observed, indicating high molecular and lamellar orientations.[13] As shown in Fig. 2(a), these various arc-like diffraction circles from inner to outer are related with different lattice planes for iPP, which are the feature of α- and β-crystal. Of note, the diffraction intensity of β(300) emerging in the middle of α(110) and α(040) gradually increases from iPP90-0 to iPP90-0.2. On the contrary, diffraction intensity of α-crystal gradually weakens with increasing β-NA content. In order to further vertify polymorphic composition, 1D-WAXD profiles were achieved, which are presented in Fig. 2(c). From 1D-WAXD profiles, as for iPP90-0, reflection peak intensity located at ca. 16.1 for β(300) is relatively weak, which is ascribed to larger number of α-row nuclei induced by strong elongation flow field, thus inhibiting generation of β-crystal. The phenomenon is very different from our previous work.[10] With elevating β-NA content, reflection peak intensity of β(300) gradually increase, together with the decay of α-crystal peaks located at 2θ=14.18°, 16.98° and 18.68°. In light of this, the generation of β-crystal in films is ascribed to the synergistic influence of β-NA and intense elongation field. Moreover, according to the methods in literature,[16] quantitative calculations of relative β-crystal content (Kβ) have been done and the results are summarized in Table 1. Clearly, it can be observed that Kβ rapidly increases with increasing β-NA loading and it arrives at a relatively maximum of ca. 0.2 wt%. This is due to the strong heterogeneous nucleation capability of β-NA, which is capable of selectively nucleating β-crystal. Meanwhile, Kα exhibits opposite tendency. This result is consistent with crystalline morphology observed by POM (Fig. S5 in ESI).
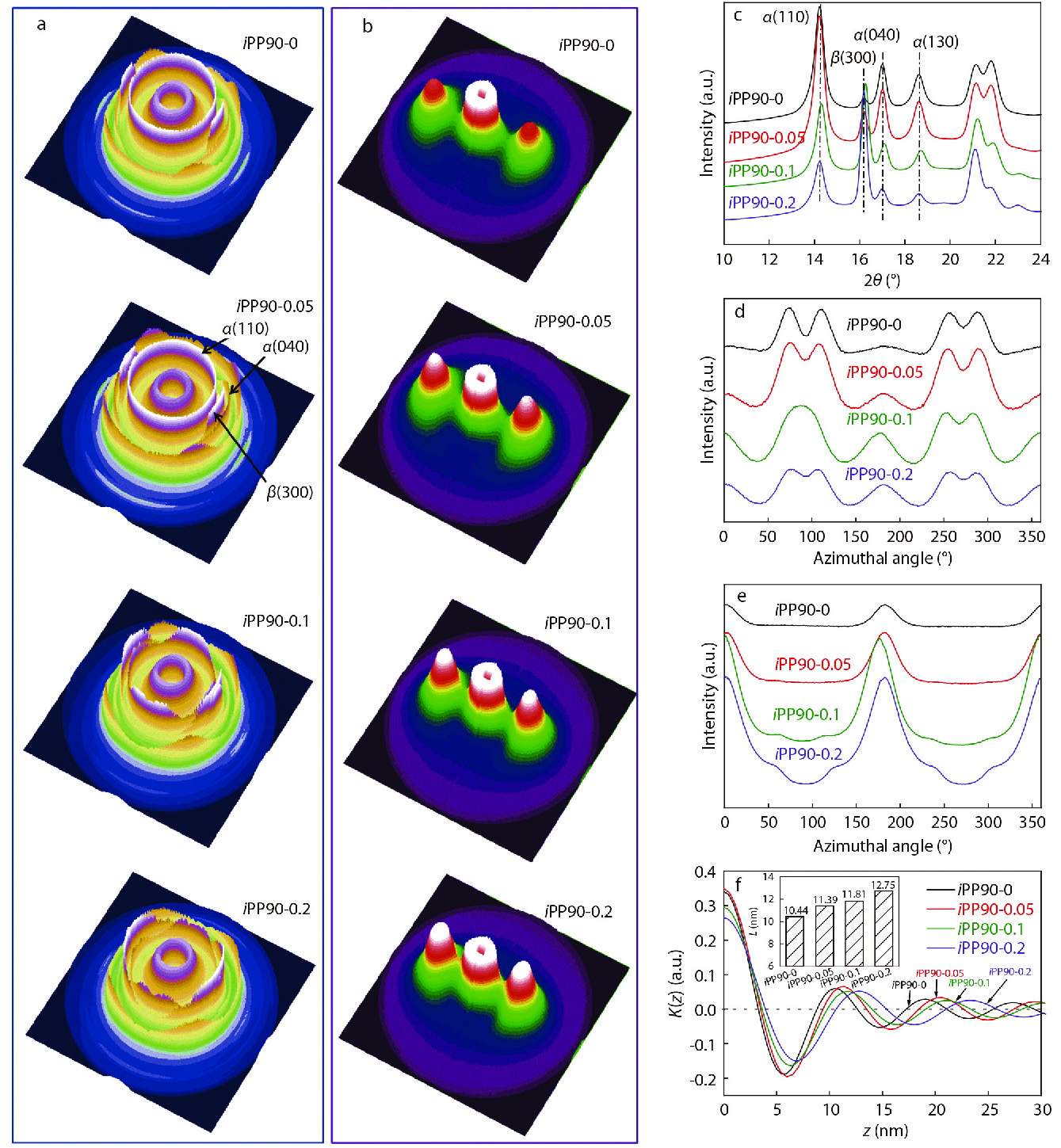
Sample | Xc (%) | Kβ (%) | Xβ (%) | Kα (%) | Xα (%) | Rα | Rβ | KD |
iPP90-0 | 47.5 | 1.7 | 0.8 | 98.3 | 46.7 | 0.8975 | − | 0.882 |
iPP90-0.05 | 46.8 | 7.0 | 3.27 | 93.0 | 43.53 | 0.8988 | − | 0.836 |
iPP90-0.1 | 43.7 | 33.7 | 14.72 | 66.3 | 28.98 | 0.7465 | 0.2245 | 0.571 |
iPP90-0.2 | 45.0 | 50.9 | 22.87 | 49.1 | 22.08 | 0.7354 | 0.2574 | 0.493 |
The azimuthal intensity curves of α- and β-crystal, i.e., α(110) and β(300) lattice planes are shown in Figs. 2(d) and 2(e). As can be seen from Fig. 2(d), the two reflection peaks at 110° and 255° should be assigned to the “daughter lamellae”, meanwhile, another peak at 180° should be attributed to “parent lamellae” of α-crystal.[17,18] Analogously, bimodal peaks situated at ca. 110° and 240° are assigned to “daughter lamellae” and the peak located at ca. 180° should be ascribed to “parent lamellae” of β-crystal (see Fig. 2e).[13,18] Moreover, there are unobvious parent-daughter structures of iPP90-0 and iPP90-0.05. Compared with iPP90-0.1, reflection peaks intensity from daughter lamellae is strongest for iPP90-0.2.[10] To get further comprehend lamellar branching, the “daughter lamellae” fractions for α- and β-crystal (Rα and Rβ)[19] and KD (i.e., relative total daughter content for α- and β-crystal) are estimated (Eq. S6 in ESI) and the calculated values are summarized in Table 1. Clearly, Rα and KD decrease with elevating β-NA content, while Rβ is apt to slightly increase, indicating that “daughter lamellae” for α- and β-crystal are prohibited. Additionally, compared with other films, L value of iPP90-0.2 is the maximum (Fig. 2f).[20] As is well known, the lamellar arrangement of β-crystal is loose, leading to larger long period than that of α-crystal.[21] Therefore, it is reasonable that larger L in iPP90-0.2 can be ascribed to higher β-crystal content. Of note, one can observe that there is a slight decrease in Xc after addition of β-NA, which may be interpreted as follows. The thickness of β-nucleated iPP films is slightly thinner than that of iPP90-0 (i.e., the thickness of iPP90-0 is about 30 μm, while the thickness of iPP90-0.2 is ca. 28 μm due to the change of viscosity (see Fig. S4 in ESI). Thin film leads to large cooling rate, and thus the effective time is short. This short effective crystallization time allows the formation of imperfect crystal,[22] thus a slight decrease in Xc for β-nucleated iPP films.
The topography of films was observed via AFM, which was carried out in tapping mode. The ex situ topography of films upon various β-NA contents are shown in Fig. 3. The top topographies represent amplitude images and those of below represent height images. Clearly, some dense spherulites are observed for iPP90-0 and iPP90-0.05 (green arrows in Fig. 3a). However, some β-crystal with loose lamellae arrangement is formed by adding β-NA (red arrows Figs. 3c and 3d). In addition, noting that the parent-daughter structure is formed in spherulites for iPP90-0.05, which is in accordance with the results in literature.[23] Meanwhile, one can also notice that lamellar arrangement and size distribution in spherulites are regular and uniform. Moreover, the lamellae interpenetrated into each other can result in enhancement of connection among lamellae. This “cross-hatched” structure influences optical properties, thermal stability, and also tensile properties of iPP products.[24-26]
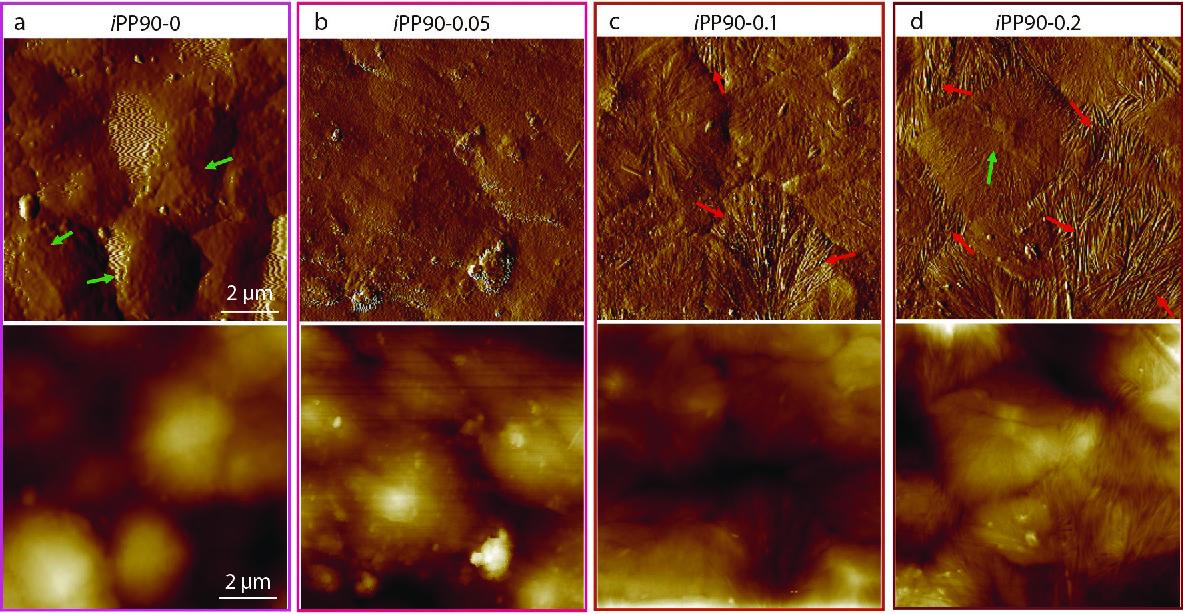
To explore the impact of various β-NA contents on crystallization behaviors of films, the morphological development of films at different temperatures during non-isothermal crystallization were investigated via POM, as shown in Fig. 4. As for iPP90-0, self-assembled iPP chains form individual homogenous dotted nuclei at about 127 °C and sporadic spherulites appear, which agrees well with the results in literature.[16] With the further cooling, there are relatively fewer large well-defined and distinct boundaries of spherulites are formed even though a high molecular and lamellar orientation level was identified in iPP90-0 before melting. This implies that oriented molecular induced by extruded-elongation in iPP90-0 completely relax upon melting. However, there exists some local order of α-crystal in melt (Fig. S6 in ESI). In our case, β-NA (i.e., WBG-II) is a kind of dispersion type nucleating agents according to the melting point of it in polymer matrix. It is established that melting point of WBG-II is as high as 240 °C,[27] therefore WBG-II granules are indissoluble or half-dissoluble in iPP under normal processing conditions (i.e., 190 °C) and it can be spontaneously self-assembled into various agglomerates. Thus incorporation of β-NA can prominently vary crystallization mode, resulting in oriented and anisotropic cylindrulites due to the self-assemble behavior of β-NA.[4] In a word, iPP chains occur on needle-like aggregate surface of β-NA, resulting in highly oriented superstructure.[27] In light of this, it is logical to infer that oriented cylindrulites induced via β-NA also exist in final films, which is responsible for tensile properties. Based on the above, due to memory effect of some local order structure around β-NA, some fine and oriented needle-like structures during early stage of crystallization (170 °C) and then cylindrulites upon further cooling are formed in β-nucleated films. Additionally, compared with iPP90-0, the considerably improved initial crystallization temperature suggests strong nucleation efficiency. Moreover, owing to the enhancement in crystallization sites, final crystal cannot be distinguished from each other and its size gradually declines with increasing β-NA content. Based on the above description, it can be concluded that β-NA can improve the crystallization rate, accompanied by the decrease of spherulite size.
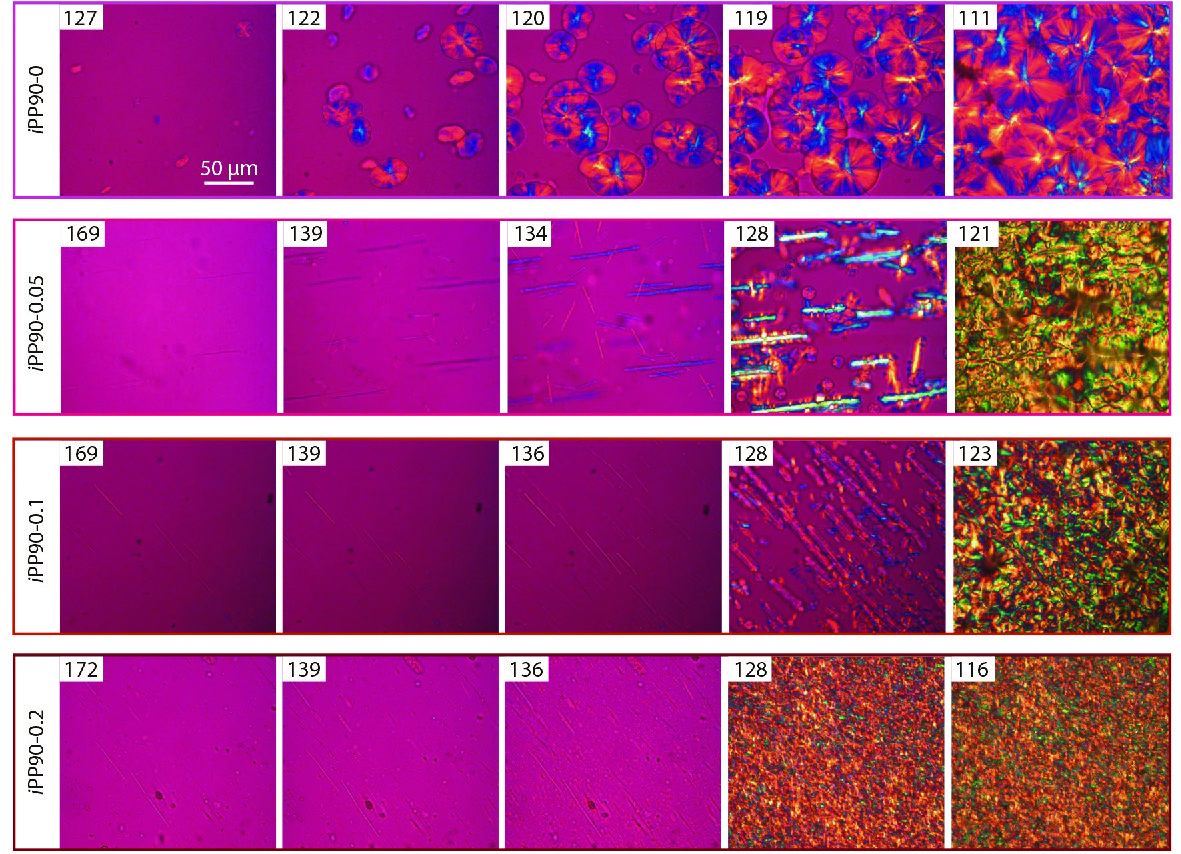
To further elucidate the influence of various β-NA contents on melting and crystallization behaviors of iPP, samples with various β-NA contents were investigated via DSC experiment. The melting curves and crystallization curves of films are shown in Fig. 5. Obviously, except for iPP90-0, three endothermic melting peaks occur in melting curves. The peaks located at ca.144 and 151 °C should be related with the fusion of β-crystal, which can be ascribed to the melting of β-crystal with different degrees of perfection and size.[2,28] That is, the peak located at 144 °C can be associated with the melting of initial β-crystal, whereas endotherm located at 150 °C is related to the melting of perfected or thickened lamellae, which is formed upon heating by partial melting and recrystallization of initially formed β-crystals. Meanwhile the dominant peak around 165 °C is ascribed to the fusion of α-crystal. Moreover, the melting peak of α-crystal slightly increases with elevating of β-NA content, demonstrating the formation of perfect crystal. Noting that there is a small shoulder peak ca.144 °C for iPP90-0, which is consistent with the aforementioned 2D-WAXD results. From Fig. 5(b), β-NA substantially affects the crystallization behavior of the samples. Based on these crystallization curves, crystallization parameters, such as peak crystallization temperature (Tp) and onset crystallization temperature (Tonset), can be achieved, which are shown in Fig. 5(c). Clearly, the values of Tonset and Tp significantly increase with the increase of β-NA content. For example, Tonset and Tp for iPP90-0 are 124.6 and 116.2 °C respectively, whereas these values rapidly increased to 135.3 and 126.4 °C for iPP90-0.2. The above results verify the efficient nucleating ability of β-NA. In addition, higher Tonset suggests a considerable decrease in supercooling (
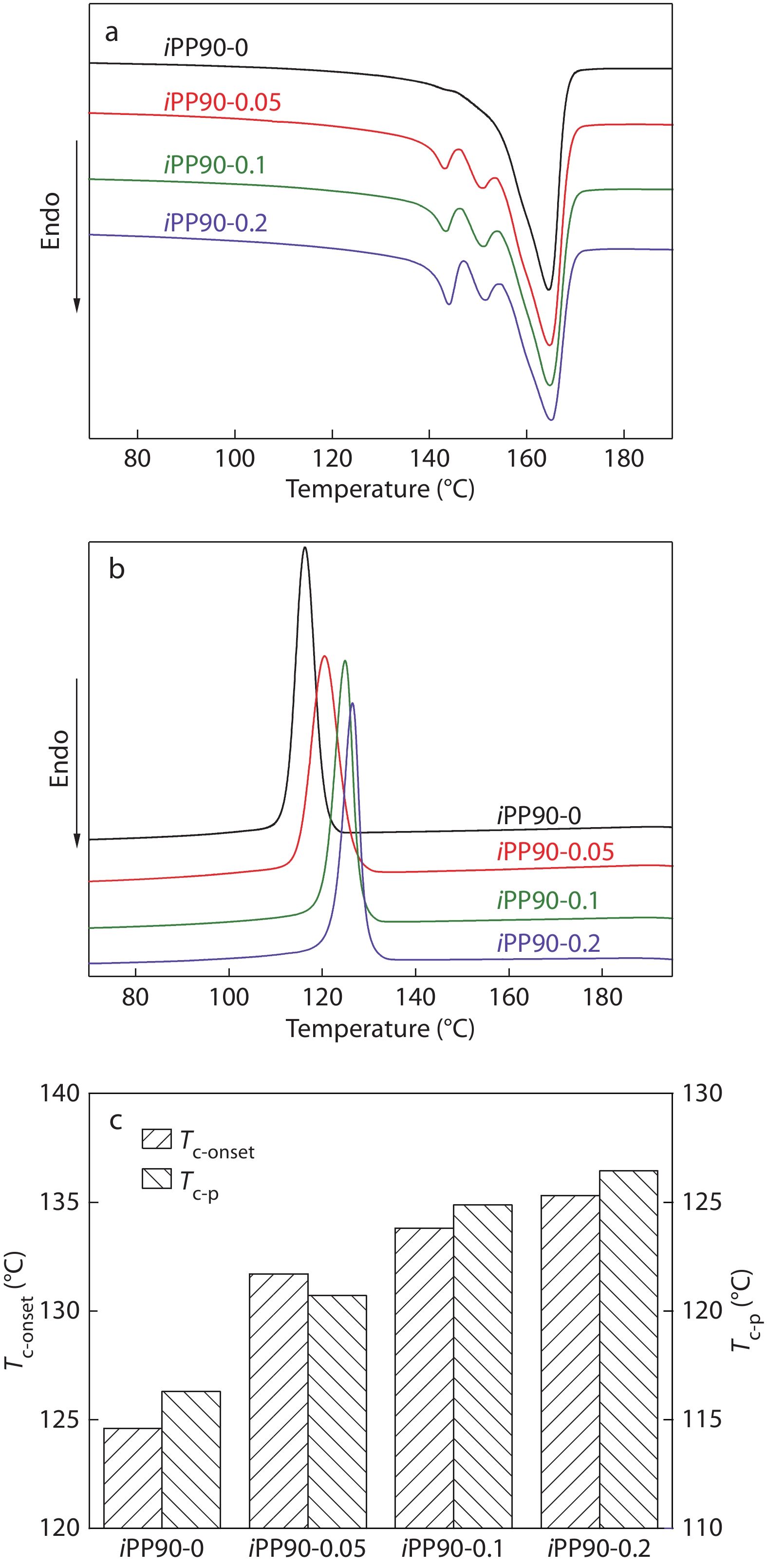
Relationship between Crystalline Structure and Tensile Properties
In our case, the σ of all films is higher than those of 35 MPa in literature.[12,14,15] This may be ascribed to extremely high orientation (Fig. S7 in ESI)[9] and obvious lamellar branching structure of α-crystal (Fig. 2d). As is well documented, branching structure is considered as interlocking structure and leads to enhanced inter-lamellar coupling, resulting in the improvement of tensile properties[30]. Compared with iPP90-0, improved toughness of β-nucleated iPP films may be ascribed to the following two parts. On one hand, increased Kβ upon introducing β-NA is beneficial to improved ε and Wb. On the other hand, during the tensile test, the phase transformation from a less (trigonal β-crystal) to a more dense (monoclinic α-crystal) crystalline structure induced via mechanical stress, accompanied with volume contraction in respect to related crystallographic densities, results in toughness improvement.[31,32] Moreover, this volume contraction prominently contributes to the void formation in general.[33] Meanwhile, during the deformation of β-nucleated iPP films, in addition to intra-lamellar and inter-lamellar slip, lamellar twisting was also observed, which also contributes to the intense voids formation.[34-36] As is well documented, voids play a crucial role in toughening polymer matrix.[37] Therefore, in our case, it is understandable that the toughness of β-nucleated iPP films is higher than that of iPP90-0. In addition, compared with iPP90-0, the σ improvement of iPP90-0.05 may be attributed to the following reasons. Firstly, larger L results in the increase of molecular chain interactions, that is, improving the fracture resistance.[38] Thus, the augment of L must be a crucial aspect for enhancement of σ. From Fig. 2(f), it can be found that L value gradually increases with rising β-NA loading, thus leading to a higher σ of iPP90-0.05 than that of iPP90-0. Secondly, numerous studies have been conducted on strengthening iPP matrix with inorganic filler.[39,40] The β-NA is also a kind of inorganic filler used for reinforcement. Briefly, some oriented iPP chains adsorbed on the surface of β-NA can be stabilized and restricted to generate oriented structure (Fig. 4), which is helpful to enhancement of σ. In addition, the σ of iPP90-0.1, and iPP90-0.2 are lower than that of iPP90-0, which is ascribed to the higher content of Kβ in β-nucleated samples and stress concentration induced by a large amount of β-NA during testing experiment.
Note that Kβ of iPP90-0.05 is lower than those of iPP90-0.1 and iPP90-0.2, while ε and Wb as well as σ of the former are higher. It is extensively recognized that β-crystal is beneficial and valid for toughening iPP. However, it is interesting that a maximum toughness was also found at certain β-NA.[41,42] In our case, tensile properties of iPP90-0.05 are higher than those of iPP90-0.1 and iPP90-0.2, which can be explained: on one hand, the toughening effect observed in iPP90-0.05 is attributed to the enhancement of connection among lamellae through the generation of “cross-hatched” structure with regular and uniform lamellae in spherulites (see Fig. 3); Moreover, β-NA can disperse uniformly in iPP melt and induce generation of β-crystal at lower β-NA content. Above critical β-NA content (i.e., 0.1 wt%), it can spontaneously self-assemble, and thus a deteriorated dispersion may cause stress concentration during testing experiment, resulting in relatively lower tensile properties.[42] Furthermore, Kβ of iPP90-0.1 and iPP90-0.2 are higher than that of iPP90-0.05, which leads to a lower σ of the former. Meanwhile, Xc and KD gradually slightly decrease with increasing β-NA content, which also results in relatively lower σ for iPP90-0.1 and iPP90-0.2.
CONCLUSIONS
In summary, iPP and β-nucleated iPP films filled with various β-NA contents are fabricated via melt-extrusion-stretched technology with intended “shear-free” in barrel and die. Subsequently, the impact of various β-NA loadings on crystalline structure and tensile properties of films were investigated. Kβ significantly increases with elevating β-NA content, whereas KD and Kα exhibit an opposite tendency. Additionally, crystallization rate is elevated along with the reducing of crystal size upon increasing β-NA content. Unexpectedly, tensile properties of iPP90-0.05 are higher than those other films. Through comprehensive analysis of crystalline structure, the notable enhancement of tensile properties for iPP90-0.05 is attributed to the combined effect of oriented structure, appropriate Kα and Kβ values and crystalline morphology. It is noteworthy that the investigation in our case gives in-depth comprehension the correlation between microstructure and tensile properties of β-nucleated iPP film fabricated under intense stretching flow field.
Structure and morphology of poly(propylenes): a molecular analysis
Polymer 1996 37 4979 4992Lotz, B.; Wittmann, J. C.; Lovinger, A. J. Structure and morphology of poly(propylenes): a molecular analysis. Polymer 1996, 37, 4979−4992.
Effect of small amount of multi-walled carbon nanotubes on crystallization and thermal-mechanical properties of overflow microinjection molded isotactic polypropylene
Compos. Commun. 2020 21 100381Liu, Z. Z.; Li, L. L.; Zheng, G. Q.; Liu, C. T.; Mi, L. W.; Li, Q.; Liu, X. H. Effect of small amount of multi-walled carbon nanotubes on crystallization and thermal-mechanical properties of overflow microinjection molded isotactic polypropylene. Compos. Commun. 2020, 21, 100381.
Studies on the α and β forms of isotactic polypropylene by crystallization in a temperature gradient
J. Polym. Sci., Part B: Polym. Phys. 1977 15 641 656Lovinger, A. J.; Chua, J. O.; Gryte, C. C. Studies on the α and β forms of isotactic polypropylene by crystallization in a temperature gradient. J. Polym. Sci., Part B: Polym. Phys. 1977, 15, 641−656.
Synergies among the self-assembled β-nucleating agent and the sheared isotactic polypropylene matrix
Polymer 2015 60 40 49Zhang, C. Y.; Wang, B.; Yang, J. H.; Ding, D. W.; Yan, X. R.; Zheng, G. Q.; Dai, K.; Liu, C. T.; Guo Z. H. Synergies among the self-assembled β-nucleating agent and the sheared isotactic polypropylene matrix. Polymer 2015, 60, 40−49.
Crystallization under shear in isotactic polypropylene containing nucleators
Polymer 2008 49 3076 3083Byelov, D.; Panine, P.; Remerie, K. Biemond, E.; Alfonso, G. C.; de Jeu, W. H. Crystallization under shear in isotactic polypropylene containing nucleators. Polymer 2008, 49, 3076−3083.
Temperature-dependent β-crystal growth in isotactic polypropylene with β-nucleating agent after shear flow
Chinese J. Polym. Sci. 2017 35 1540 1551Chen, Y. H.; Yang, H. Q.; Yang, S.; Zhang, Q. Y.; Li, Z. M. Temperature-dependent β-crystal growth in isotactic polypropylene with β-nucleating agent after shear flow. Chinese J. Polym. Sci. 2017, 35, 1540−1551.
Effect of solubility and nucleating duality of N,N'-dicyclohexyl-2,6-naphthalenedicarboxamide on the supermolecular structure of isotactic polypropylene
Macromolecules 2007 40 2422 2431Varga, J.; Menyhárd, A. Effect of solubility and nucleating duality of N,N'-dicyclohexyl-2,6-naphthalenedicarboxamide on the supermolecular structure of isotactic polypropylene. Macromolecules 2007, 40, 2422−2431.
Superior reinforcement in melt-spun polyethylene/multiwalled carbon nanotube fiber through formation of a shish-kebab structure
J. Phys. Chem. B 2010 114 10693 10702Mai, F.; Wang, K.; Yao, M. J.; Deng H.; Chen, F.; Fu, Q. Superior reinforcement in melt-spun polyethylene/multiwalled carbon nanotube fiber through formation of a shish-kebab structure. J. Phys. Chem. B 2010, 114, 10693−10702.
Molecular orientation and mechanical anisotropy of polypropylene sheet containing N,N'-dicyclohexyl-2,6-naphthalenedicarboxamide
J. Polym. Sci., Part B: Polym. Phys. 2009 47 424 433Uchiyama, Y.; Iwasaki, S.; Ueoka, C.; Fukui, T.; Okamoto, K.; Yamaguchi, M. Molecular orientation and mechanical anisotropy of polypropylene sheet containing N,N'-dicyclohexyl-2,6-naphthalenedicarboxamide. J. Polym. Sci., Part B: Polym. Phys. 2009, 47, 424−433.
Mechanical enhancement of melt-stretched β-nucleated isotactic polypropylene: the role of lamellar branching of β-crystal
Polym. Test. 2017 58 227 235Liu, Z. Z.; Liu, X. H.; Zheng, G. Q.; Dai, K.; Liu, C. T.; Shen, C. Y.; Yin, R.; Guo Z. H. Mechanical enhancement of melt-stretched β-nucleated isotactic polypropylene: the role of lamellar branching of β-crystal. Polym. Test. 2017, 58, 227−235.
Negative effect of stretching on the development of β-phase in β-nucleated isotactic polypropylene
Polym. Int. 2011 60 1016 1023Zheng, G. Q.; Li, S. W.; Zhang, X. L.; Liu, C. T.; Dai, K.; Chen, J. B.; Li, Q.; Peng, X. F.; Shen, C. Y. Negative effect of stretching on the development of β-phase in β-nucleated isotactic polypropylene. Polym. Int. 2011, 60, 1016−1023.
Facilely assess the soluble behaviour of the β-nucleating agent by gradient temperature field for the construction of heterogeneous crystalline-frameworks in iPP
Soft Matter. 2015 12 594 601Wu, Z. Q.; Wang, G.; Zhang, M. W.; Wang, K.; Fu, Q. Facilely assess the soluble behaviour of the β-nucleating agent by gradient temperature field for the construction of heterogeneous crystalline-frameworks in iPP. Soft Matter. 2015, 12, 594−601.
Crystalline structure and remarkably enhanced tensile property of β-isotactic polypropylene via overflow microinjection molding
Polym. Test. 2019 76 448 454Liu, Z. Z.; Liu, X. H.; Li, L. L.; Zheng, G. Q.; Liu, C. T.; Qin, Q.; Mi, L. W. Crystalline structure and remarkably enhanced tensile property of β-isotactic polypropylene via overflow microinjection molding. Polym. Test. 2019, 76, 448−454.
Combined effect of chemically compound graphene oxide-calcium pimelate on crystallization behavior, morphology and mechanical properties of isotactic polypropylene
Polym. Adv. Technol. 2020 31 2301 2311Zhang, Y. F.; Lin, X. F.; Hu, H. Combined effect of chemically compound graphene oxide-calcium pimelate on crystallization behavior, morphology and mechanical properties of isotactic polypropylene. Polym. Adv. Technol. 2020, 31, 2301−2311.
Synergistic nucleation effect of calcium sulfate whisker and β-nucleating agent dicyclohexyl-terephthalamide in isotactic polypropylene
J. Therm. Anal. Calorim. 2020 139 343 352Zhang, Y. F.; Lin, X. F.; Yan, L.; Li, Y.; He, B. Synergistic nucleation effect of calcium sulfate whisker and β-nucleating agent dicyclohexyl-terephthalamide in isotactic polypropylene. J. Therm. Anal. Calorim. 2020, 139, 343−352.
Nucleating agents based on graphene and graphene oxide for crystallization of the β-form of isotactic polypropylene
J. Mater. Sci. 2020 55 1436 1450Broda, J.; Baczek, M.; Fabia, J.; Binias, D.; Fryczkowski, R. Nucleating agents based on graphene and graphene oxide for crystallization of the β-form of isotactic polypropylene. J. Mater. Sci. 2020, 55, 1436−1450.
Crystalline structure of injection molded β-isotactic polypropylene analysis of the oriented shear zone
Ind. Eng. Chem. Res. 2013 52 11996 12002Liu, X. H.; Dai, K.; Hao, X. Q.; Zheng, G. Q.; Liu, C. T.; Schubert, D. W.; Shen, C. Y. Crystalline structure of injection molded β-isotactic polypropylene analysis of the oriented shear zone. Ind. Eng. Chem. Res. 2013, 52, 11996−12002.
New insight into lamellar branching of β-nucleated isotactic polypropylene upon melt-stretching: WAXD and SAXS study
J. Mater. Sci. 2015 50 599 604Liu, Z. Z.; Liu, X. H.; Liu, C. T.; Shen, C. Y.; Dai, K.; Zheng, G. Q. New insight into lamellar branching of β-nucleated isotactic polypropylene upon melt-stretching: WAXD and SAXS study. J. Mater. Sci. 2015, 50, 599−604.
Structure of skin layer in injection-molded polypropylene
J. Appl. Polym. Sci. 2010 35 29 49Fujiyama, M.; Wakino, T.; Kawasaki, Y. Structure of skin layer in injection-molded polypropylene. J. Appl. Polym. Sci. 2010, 35, 29−49.
Later stage melting of isotactic polypropylene
Macromolecules 2020 53 2136 2144Shen, J. F.; Zhou, Y. F.; Lu, Y.; Wang, B. H.; Shen, C. Y.; Chen, J. B.; Zhang, B. Later stage melting of isotactic polypropylene. Macromolecules 2020, 53, 2136−2144.
Combined effect of shear and fibrous fillers on orientation-induced crystallization in discontinuous aramid fiber/isotactic polypropylene composites
Polymer 2008 49 295 302Larin, B.; Avila-Orta, C. A.; Somani, R. H.; Hsiao, B. S.; Marom, G. Combined effect of shear and fibrous fillers on orientation-induced crystallization in discontinuous aramid fiber/isotactic polypropylene composites. Polymer 2008, 49, 295−302.
Heterogeneous nucleation and self-nucleation of poly(p-dioxanone)
J. Mater. Sci. 2000 35 5071 5084Sabino, M. A.; Ronca, G.; Müller, A. J. Heterogeneous nucleation and self-nucleation of poly(p-dioxanone). J. Mater. Sci. 2000, 35, 5071−5084.
Microstructure characterization in a single isotactic polypropylene spherulite by synchrotron microfocus wide angle X-ray scattering
Polymer 2018 142 387 393Chang, B. B.; Schneider, K.; Patil, N.; Stephan, R.; Gert, H. Microstructure characterization in a single isotactic polypropylene spherulite by synchrotron microfocus wide angle X-ray scattering. Polymer 2018, 142, 387−393.
Polymer spherulites: a modern assessment
J. Macrom. Sci., Part B 2003 42 227 256Bassett, D. C. Polymer spherulites: a modern assessment. J. Macrom. Sci., Part B 2003, 42, 227−256.
The spherulitic and lamellar morphology of melt-crystallized isotactic polypropylene
Polymer 1985 26 704 716Norton, D. R.; Keller, A. The spherulitic and lamellar morphology of melt-crystallized isotactic polypropylene. Polymer 1985, 26, 704−716.
In situ synchrotron X-ray scattering studies on the temperature dependence of oriented β-crystal growth in isotactic polypropylene
Polym. Test. 2020 90 106660Quan, L. J.; Zhang, X. D.; Xia, W. L.; Chen, Y. H.; Gong, L.; Liu, Z. G.; Zhang, Q. Y.; Zhong, G. J.; Li, Z. M.; Hsiao, B. S. In situ synchrotron X-ray scattering studies on the temperature dependence of oriented β-crystal growth in isotactic polypropylene. Polym. Test. 2020, 90, 106660.
New understanding in tuning toughness of β-polypropylene: the role of β-nucleated crystalline morphology
Macromolecules 2009 42 9325 9331Luo, F.; Geng, C. Z.; Wang,; Deng, H.; Chen, F.; Fu, Q.; Na, B. New understanding in tuning toughness of β-polypropylene: the role of β-nucleated crystalline morphology. Macromolecules 2009, 42, 9325−9331.
Microstructure and mechanical properties of isotactic polypropylene films fabricated via melt-extrusion and uniaxial-stretching
J. Macromol. Sci., Part B Phys. 2016 55 158 174Liu, Z. Z.; Zheng, G. Q.; Zheng, H. L.; Dai, K.; Liu, C. T.; Chen, J. B.; Shen, C. Y. Microstructure and mechanical properties of isotactic polypropylene films fabricated via melt-extrusion and uniaxial-stretching. J. Macromol. Sci., Part B Phys. 2016, 55, 158−174.
Role of reptation in the rate of crystallization of polyethylene fractions from the melt
Polymer 1982 23 656 670Hoffman, J. D. Role of reptation in the rate of crystallization of polyethylene fractions from the melt. Polymer 1982, 23, 656−670.
Viscous-force-dominated tensile deformation behavior of oriented polyethylene
Macromolecules 2006 39 2584 2591Na, B.; Zhang, Q.; Fu, Q. Viscous-force-dominated tensile deformation behavior of oriented polyethylene. Macromolecules 2006, 39, 2584−2591.
Effects of β-α transformation on the static and dynamic tensile behavior of isotactic polypropylene
J. Appl. Polym. Sci. 1998 62 291 300Karger-Kocsis, J.; Varga, J. Effects of β-α transformation on the static and dynamic tensile behavior of isotactic polypropylene. J. Appl. Polym. Sci. 1998, 62, 291−300.
How does "phase transformation toughening" work in semicrystalline polymers?
Polym. Eng. Sci. 2010 36 203 210Karger-Kocsis, J. How does "phase transformation toughening" work in semicrystalline polymers? Polym. Eng. Sci. 2010, 36, 203−210.
Microvoid formation process during the plastic deformation of β-form polypropylene
Polymer 1994 35 3442 3448Chu, F.; Yamaoka, T.; Ide, H.; Kimura, Y. Microvoid formation process during the plastic deformation of β-form polypropylene. Polymer 1994, 35, 3442−3448.
Molecular deformation mechanisms of isotactic polypropylene in α- and β-crystal forms by FTIR spectroscopy
J. Polym. Sci., Part B: Polym. Phys. 2004 42 4478 4488Huy, T.; Adhikari, R.; Lüpke, T.; Henning, S.; Michler, G. H. Molecular deformation mechanisms of isotactic polypropylene in α- and β-crystal forms by FTIR spectroscopy. J. Polym. Sci., Part B: Polym. Phys. 2004, 42, 4478−4488.
Influence of nucleating agent self-assembly on structural evolution of isotactic polypropylene during uniaxial stretching
Polymer 2018 138 329 342Chang, B. B.; Schneider, K.; Vogel, R.; Heinrich, G. Influence of nucleating agent self-assembly on structural evolution of isotactic polypropylene during uniaxial stretching. Polymer 2018, 138, 329−342.
Deformation induced void formation and growth in β nucleated isotactic polypropylene
Polymer 2019 178 121523Kawai, T.; Soeno, S.; Kuroda, S. I.; Kuroda, S. I.; Koido, S.; Nemoto, T.; Tamada, M. Deformation induced void formation and growth in β nucleated isotactic polypropylene. Polymer 2019, 178, 121523.
Realizing the simultaneously improved toughness and strength of ultra-thin LLDPE parts through annealing
Polymer 2013 54 6843 6852Shi, S. Y.; Pan, Y. M.; Lu, B.; Zheng, G. Q.; Liu, C. T.; Dai, K.; Shen, C. Y. Realizing the simultaneously improved toughness and strength of ultra-thin LLDPE parts through annealing. Polymer 2013, 54, 6843−6852.
Simultaneously improving tensile strength and toughness of melt-spun β-nucleated isotactic polypropylene fibers
J. Appl. Polym. Sci. 2016 133 43454Liu, Z. Z.; Zheng, G. Q.; Dai, K.; Liu, C. T,; Shen, C. Y. Simultaneously improving tensile strength and toughness of melt-spun β-nucleated isotactic polypropylene fibers. J. Appl. Polym. Sci. 2016, 133, 43454.
Experimental investigation on mechanical characteristics of composite reinforced cantala fiber (CF) subjected to microcrystalline cellulose and fumigation treatments
Compos. Commun. 2020 21 100419Sakuri, S.; Surojo, E.; Ariawan, D. Experimental investigation on mechanical characteristics of composite reinforced cantala fiber (CF) subjected to microcrystalline cellulose and fumigation treatments. Compos. Commun. 2020, 21, 100419.
Investigation of improvement of properties of polypropylene modified by nano silica composites
Compos. Commun. 2019 12 59 63Awad, S. A.; Khalaf, E. M. Investigation of improvement of properties of polypropylene modified by nano silica composites. Compos. Commun. 2019, 12, 59−63.
Structure and properties of injection moldings of β-crystal nucleator-added PP
Int. Polym. Process. 1998 13 291 298Fujiyama, M. Structure and properties of injection moldings of β-crystal nucleator-added PP. Int. Polym. Process. 1998, 13, 291−298.
Dependence of mechanical properties on β-form content and crystalline morphology for β-nucleated isotactic polypropylene
Polym. Adv. Technol. 2011 22 2044 2054Luo, F.; Wang, K.; Ning, N. Y.; Geng, C. Z. Dependence of mechanical properties on β-form content and crystalline morphology for β-nucleated isotactic polypropylene. Polym. Adv. Technol. 2011, 22, 2044−2054.